While today there is an ever-increasing array of jewelry designs available, having the only one in the world of a ring, bracelet, or necklace holds huge appeal. There are two ways to approach this: One is to purchase a pre-made custom piece from a designer who creates their own one-of-a-kind designs. The other option is to work with a designer who will work with you to create custom jewelry.
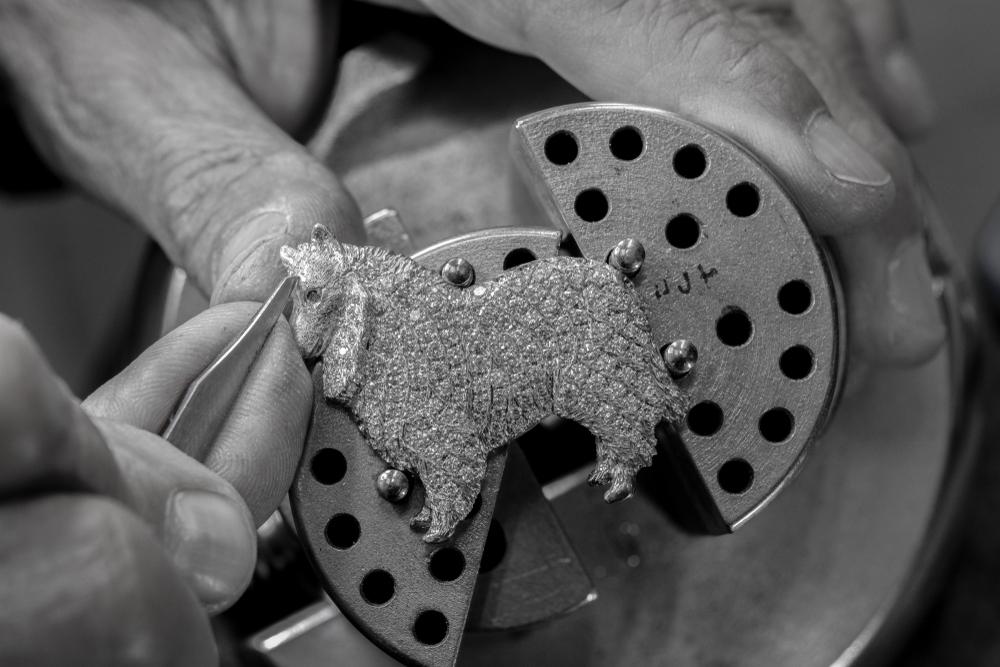
Art You Can Wear
For 32 years, Mark Lloyd, owner of Vanmark Jewelry in Fort Lauderdale, Florida, has been creating wearable works of art. Well-known for his sport fish-themed jewelry, Lloyd also accepts custom projects.“My goal is to create jewelry that perfectly matches my client’s expectations,” he said. “We’ll start with an overview of what they want. I’ll ask questions to fine-tune the overall design and show them a sketch of how it will look. I’ll also provide an estimate of the total cost to make sure it is in line with their budget. When I see their eyes light up as they look at the sketch, I know we’re ready to make it a reality.”
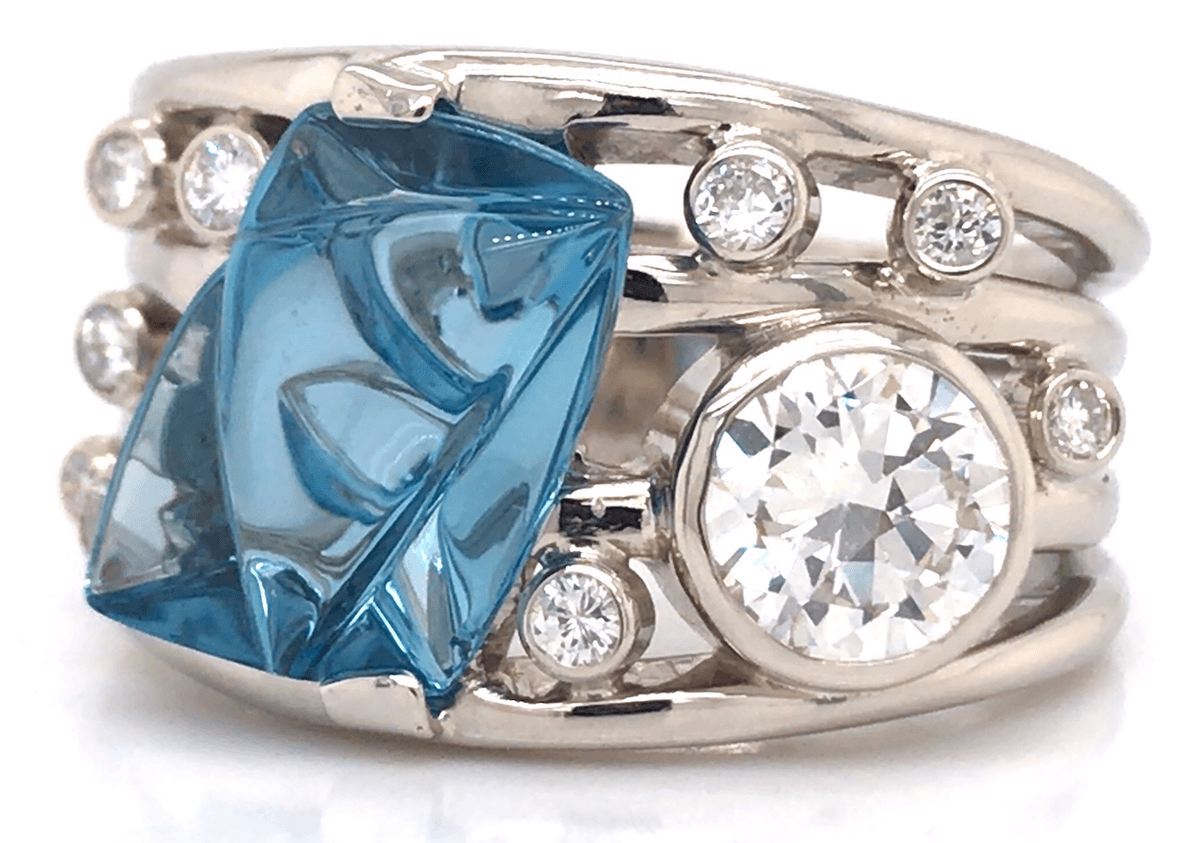
Unique Designs
Another designer who creates custom jewelry, as well as his own designs, is Robert Pelliccia, whose works are exclusively sold by JR Dunn Jewelers in Lighthouse Point, Florida.“We use Pinterest to get ideas to kickstart the design process, such as finding elements from a number of different pieces,” he said. “We then refine the design until it is perfect.”
“I can create new jewelry using readily available jewels and metals, but many of my customers ask me to use precious metals and gemstones from jewelry they’ve inherited or pieces they no longer wear,” Lloyd said. “This way they get new jewelry that already has sentimental value.”
During this phase, the designer will work closely with the customer to ensure the precious metals provided will create the perfect outcome.
“If I’m working with platinum, silver, or various purities of gold, I’ll make sure the color of the finished piece will be exactly what they expect,” he said. “I’ll also use this time to determine the font and size of any engraving as well as the texture or finish desired.”
How Custom Jewelry Is Made
There are two ways to create custom jewelry.“You can use the lost wax method or fabrication,” Lloyd said. “About 90 percent of my custom works are made using the lost wax method.”
As a broad overview, the process begins with the designer carving a wax model of the piece. Some designers use a 3-D printer to create the wax model. The wax model is then placed in a cylinder into which plaster is added. Care must be taken to ensure there are no bubbles in the plaster, which could distort the finished jewelry.
The investment is placed in a kiln overnight, during which time the wax model is vaporized, leaving a negative mold. The next day the metal can be melted and poured into the mold.
When the plaster mold is “quenched” in cool water, the plaster dissolves, revealing the jewelry. At this point, the piece is cleaned and polished, and stones can be set if needed. Lloyd says the alternative fabrication process is less time-consuming as it allows the designer to use pre-made components and findings, individual pieces such as a fastener for a pendant. However, he and Pelliccia both prefer using the lost wax method.
If the design utilizes gemstones, Lloyd prefers to mount them while the customer observes. “The customer needs to trust their jeweler implicitly. In order to preserve that trust and avoid any possibility of a question as to the customers’ gems being used, I will inspect and measure them during the design phase with the customer, asking the customer to bring them back when I’m ready to set them,” he said.
“In cases where I need to keep the gemstones in my possession, I’ll use a loupe to show the customer any flaws that identify the stones, providing a sketch they can use to confirm the same stones are in the finished piece.”
Creating a custom piece of jewelry might seem to be fraught with the potential for the finished piece to differ from the initial vision. However, Lloyd and Pelliccia agree that by working closely with the customer during the design phase and allowing them to view the wax model prior to casting, the finished piece has always turned out perfect.