There’s something special about getting a bespoke item made just for your body. True bespoke craftsmanship tailors to the human form, and while this kind of fashion may cost more than fast fashion, it’s sustainable, unique, and money-saving in the long run.
In the small town of Baden-Baden in southwest Germany, Vickermann and Stoya, a bespoke cobbler, is making famous a craft that’s hard to find in 2022.
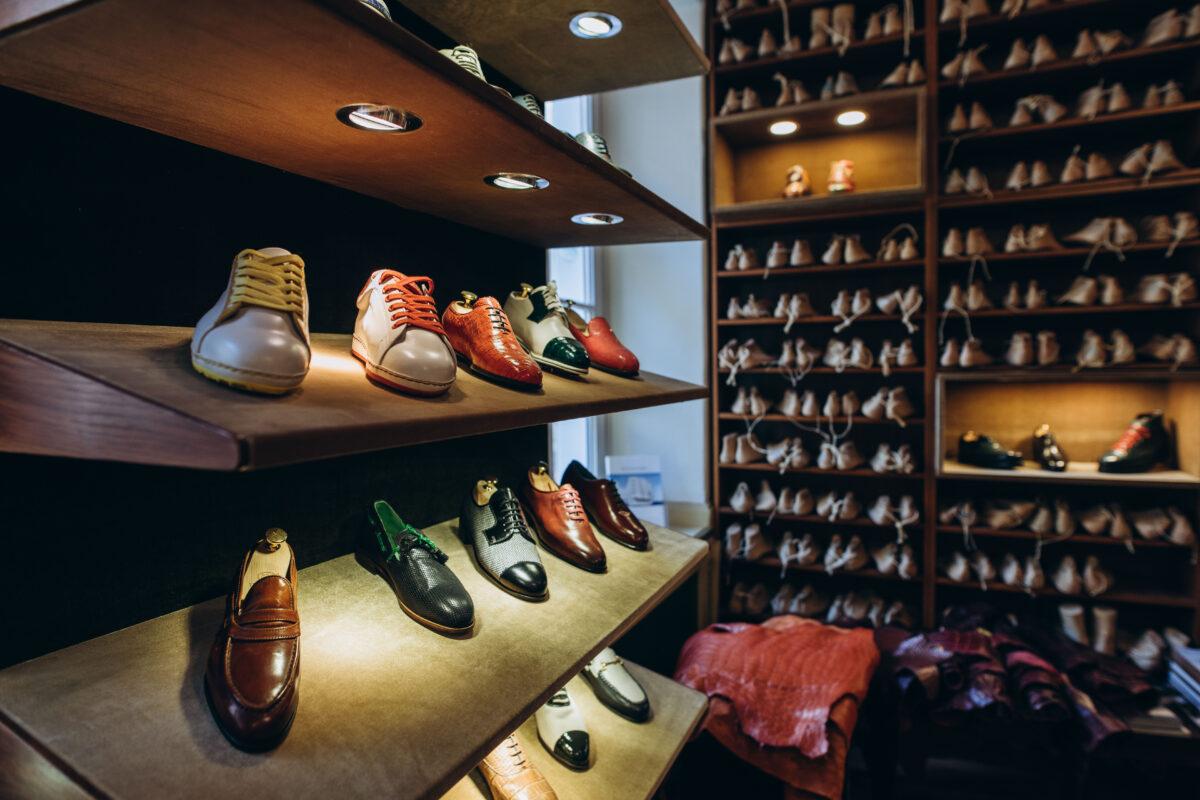
Bespoke shoemaking was popular well into the 19th century. Customers would visit a shop, have their measurements and requests taken, and return at a later date to pick up their custom footwear. Industrialization morphed into industrial mass production and forever changed shoemaking, turning bespoke shoes into a rarity. Many of today’s shoes don’t carry the same high-quality, traditional craftsmanship skills and attention to detail they once did.
Matthias Vickermann and Martin Stoya understand the value of traditional shoemaking. They make and repair shoes for men, women, and children all over the world. It’s a distinct skill, “and we do a lot to preserve this craft,” said Vickermann. He knows that manufacturers in Germany can’t easily hold their own in the market but that German and international clientele want to support the craft.
Vickermann learned shoemaking in a small workshop in Baden-Baden. Before that, he was a trained accountant but decided to go in a different direction and pursue this craft. “I have shoe size 50 [U.S. men’s size 15 1/2] and already liked to wear nice shoes at that time,” he said. “I found it interesting to get insight into the industry, and I don’t regret my decision today.” With his background, he handles much of the business side of the company.
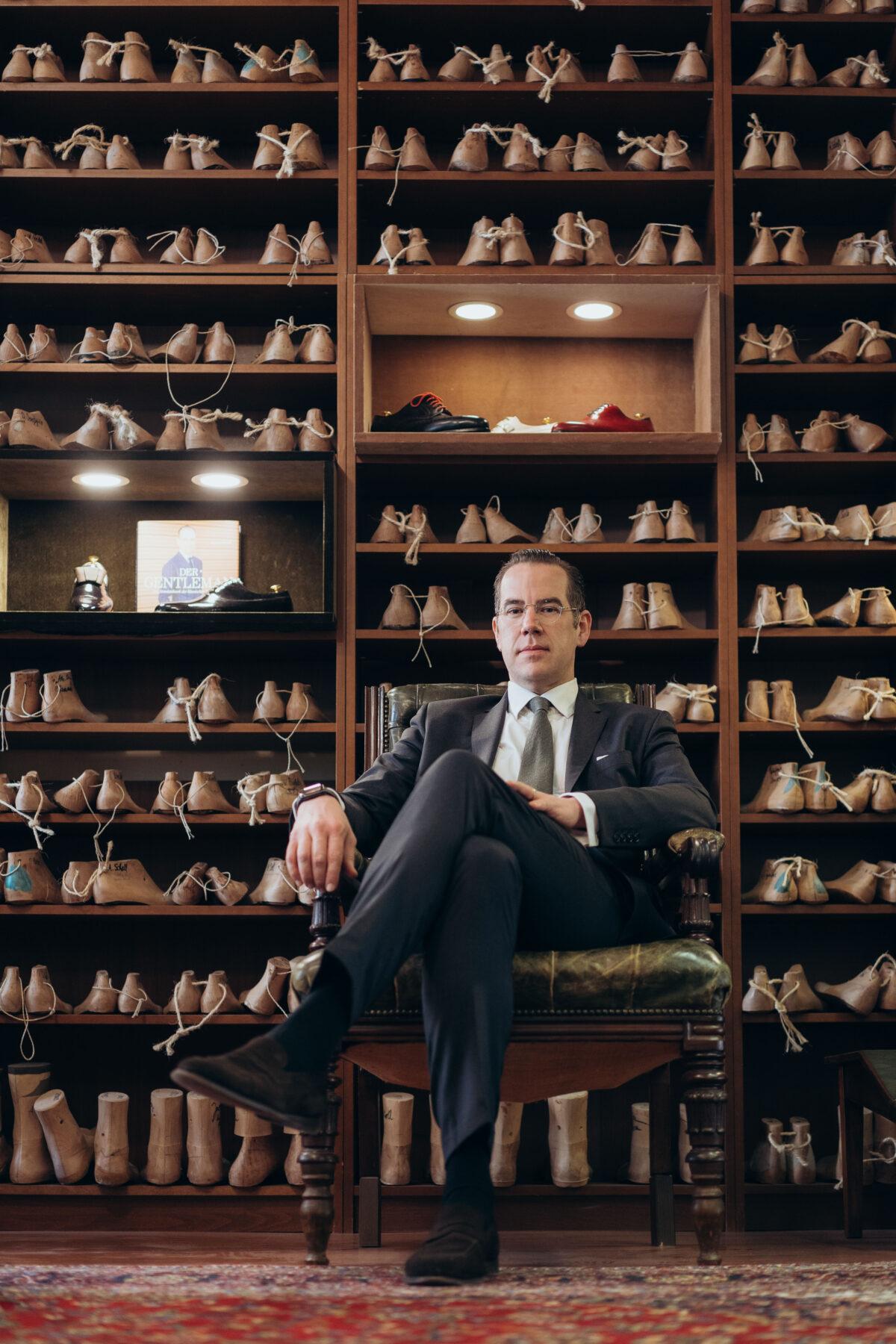
Courtesy of Vickermann und Stoya
Stoya is a trained orthopedic shoemaker, but learned during his training about traditional hand sewing methods. He brings both to his work: “What is special about us is that the orthopedic details are also taken into account, so that both specialties are combined in one, and the shoes fit like a second skin,” he said. He can always be found in the workshop with an apron on, repairing a pair of shoes or handmaking a new one with specialized orthopedic elements.
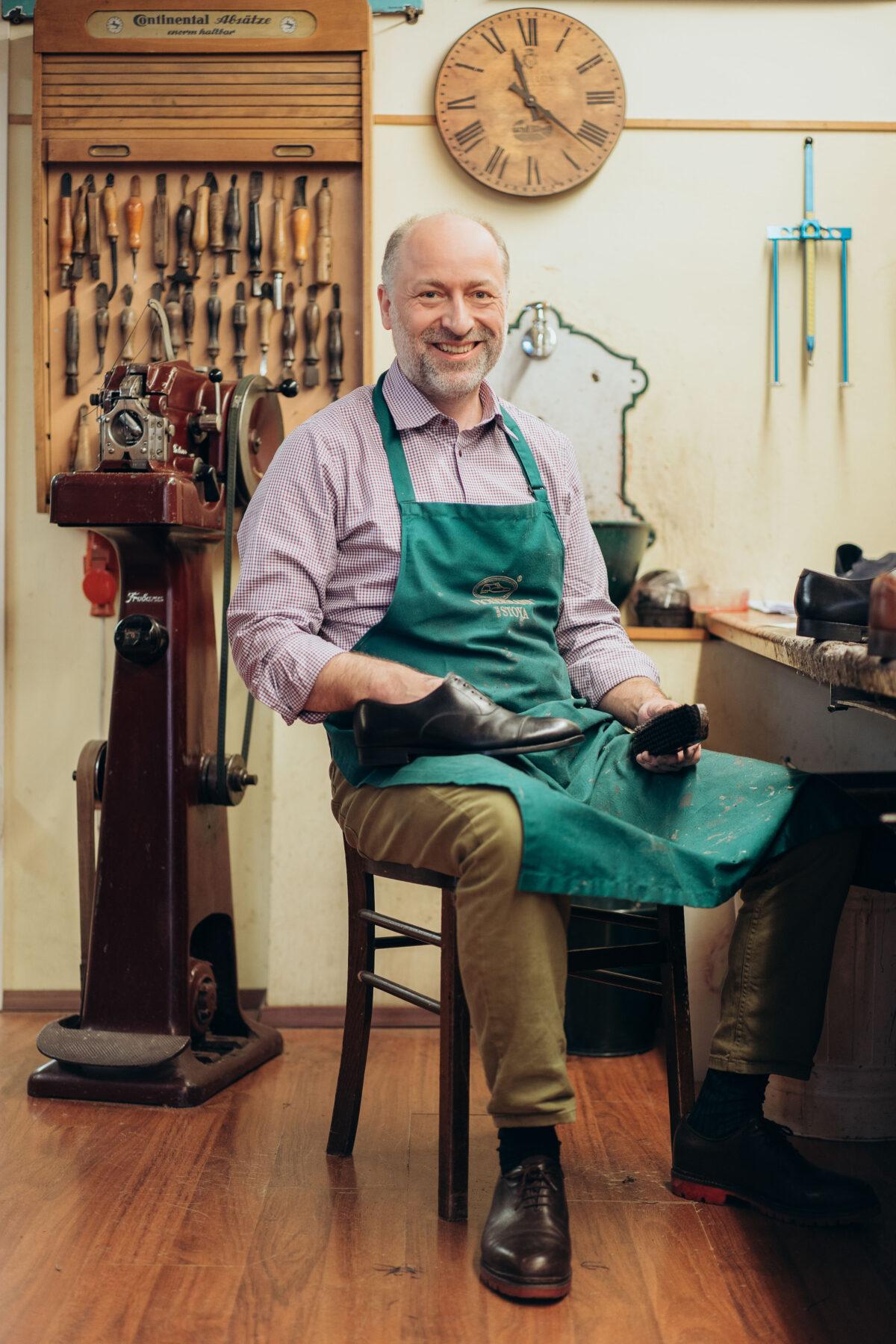
Courtesy of Vickermann und Stoya
The Making of a Shoe
Walking into their store, set in a historical German edifice, customers are met with views of the open workshop, which allows them to watch the shoemakers at work, surrounded by various shoe styles and other leather accessories on display. On the floor above are offices, a shoeshine salon, and a bar where seminars often take place.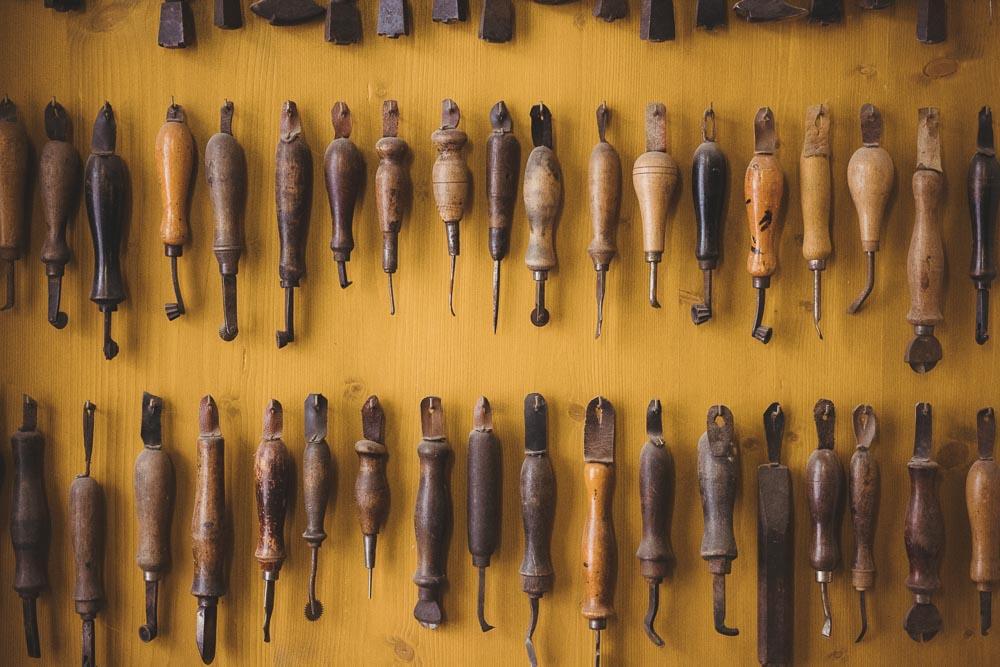
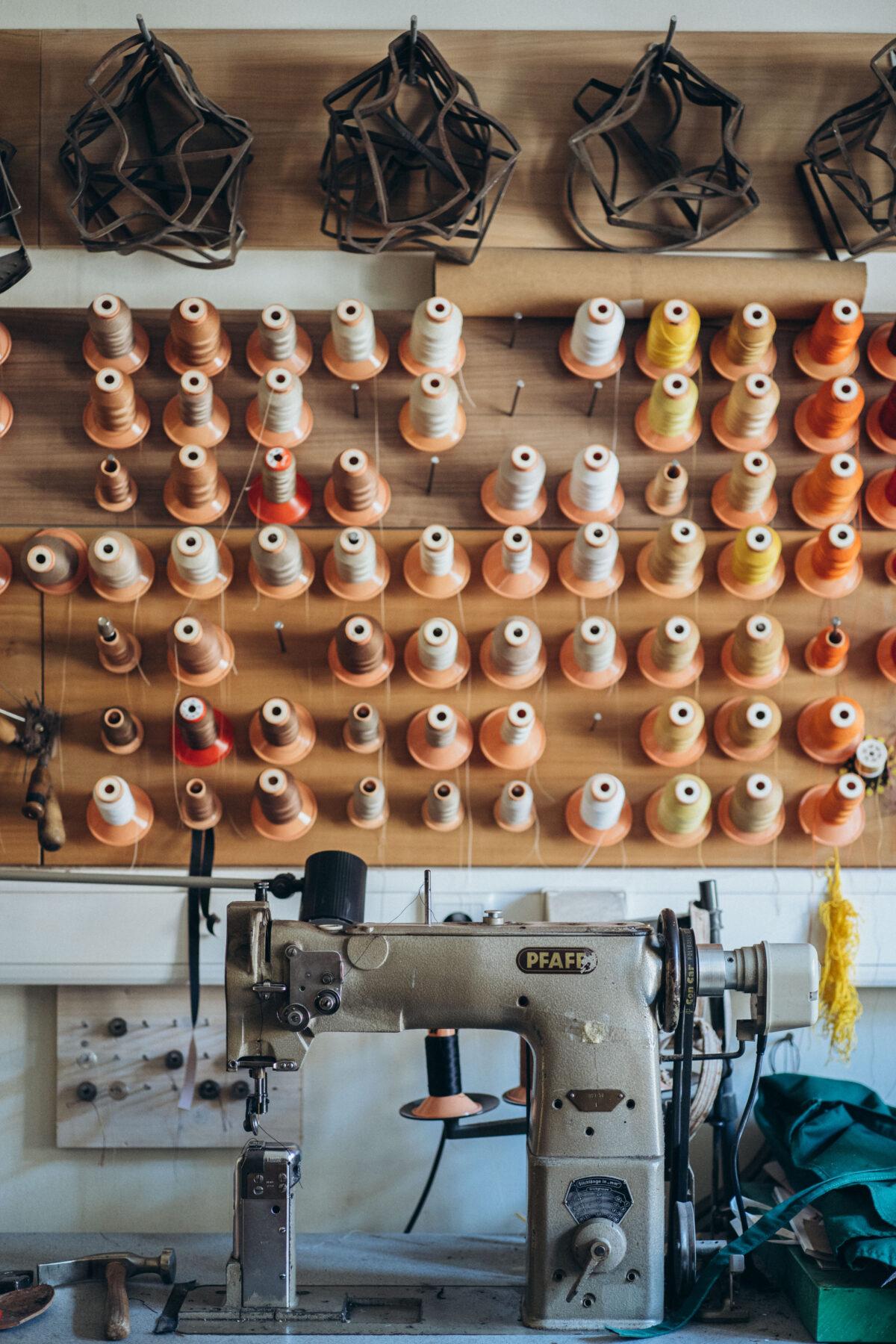
Every pair of shoes starts with Vickermann taking measurements, including each foot’s pressure points and circumferences—of the heel, ankle, instep, ball, and toes.
The customer chooses his desired shoe style and selects the leather and color, from options ranging from classic calfskin to ostrich or other exotic skins. This is where “the conversation gets interesting,” Vickermann said. “Honest customer advice is very important to us, and we also take a lot of time for this.”
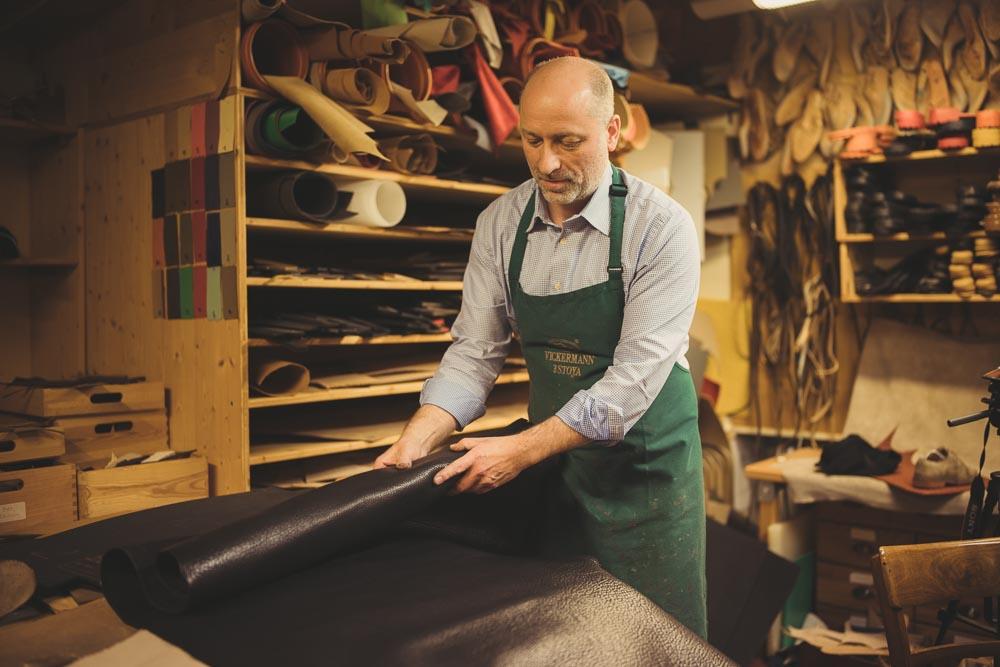
From this information, they create the lasts, or shoe molds. They order raw lasts, which are much larger than needed, and reduce them to the proper foot size and shape them by grinding to the desired form.
“The biggest difficulty is bringing together the measurements and the form,“ Stoya said. They must precisely match the customer’s measurements so that everything fits perfectly in the end. ”This step can take from one to four hours.”
A trial pair of shoes is made from simple leather, and the customer is instructed to wear these for two weeks. The impressions and markings made by their feet during this trial period will help the shoemaker see details such as where the fit is not exact, how far the lacing is opened, how the foot stretches or swells during the day, and how the customer walks.
“The customer then gives us feedback, and if necessary, the lasts must be modified again,” Stoya said. Then they begin assembling the actual shoes.
The customer’s model is constructed from paper templates, and proportions are checked. The insole is created, then individual pieces are cut from the selected leather to construct the upper leather, which is later shaped and pinched over the last. The leather and insole are sewn together by hand, and after the shoe is air-dried, the soles and heels are built out layer by layer.
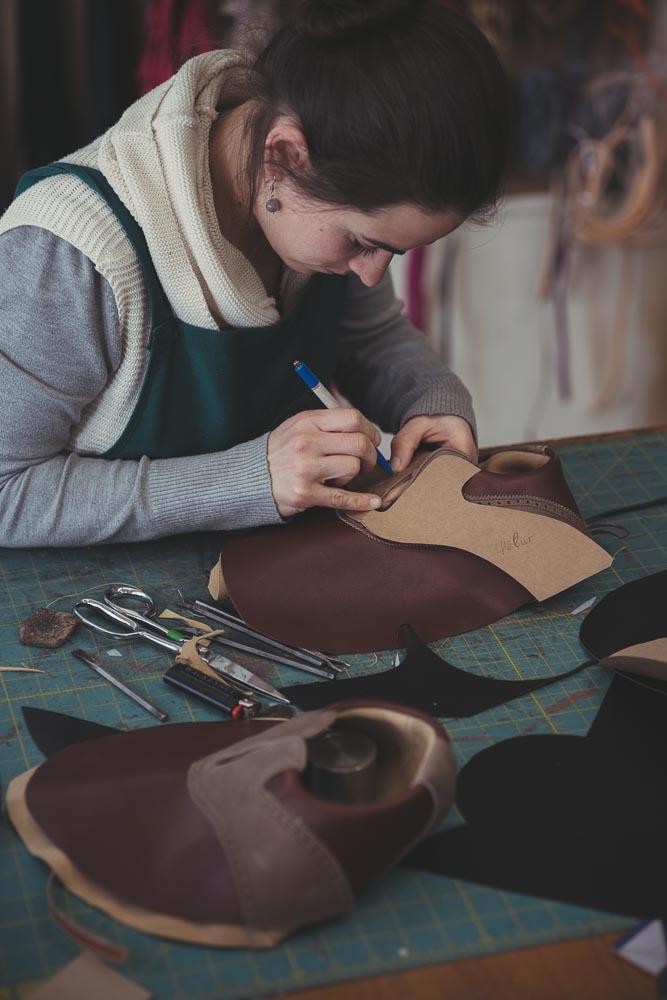
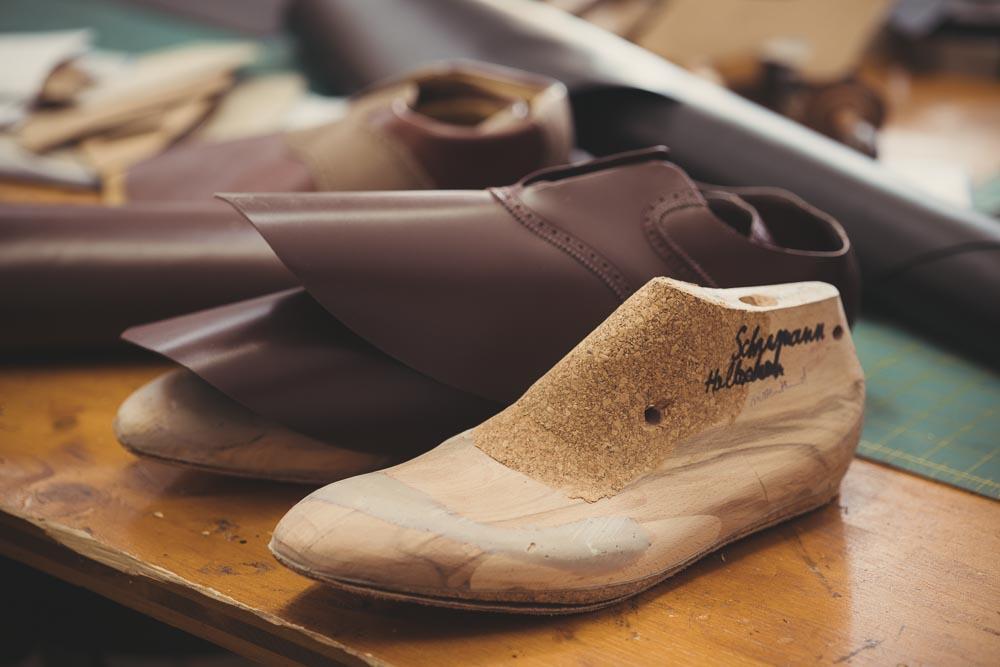
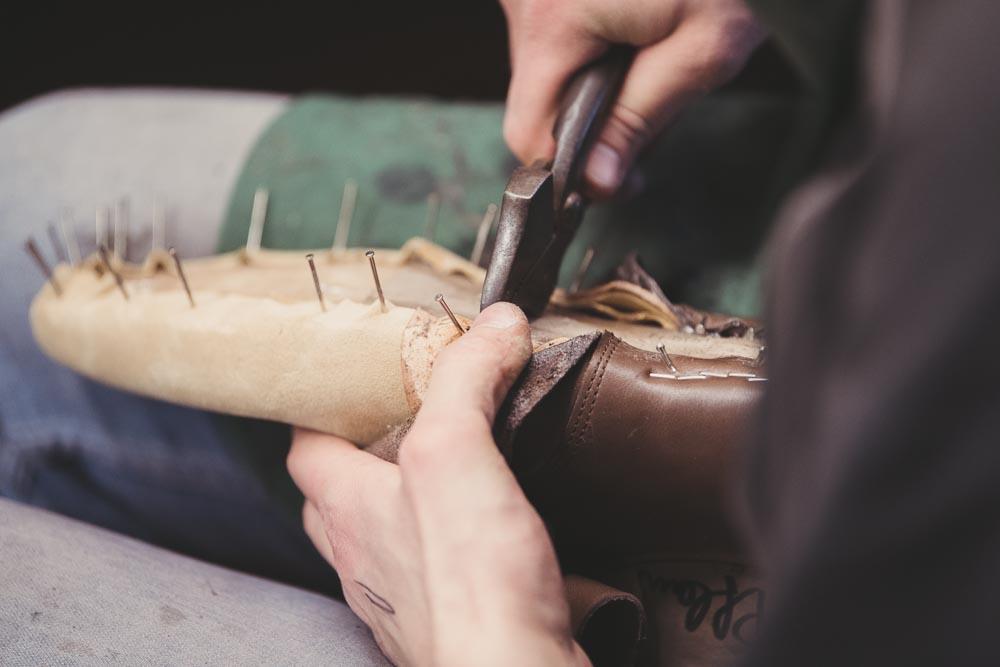
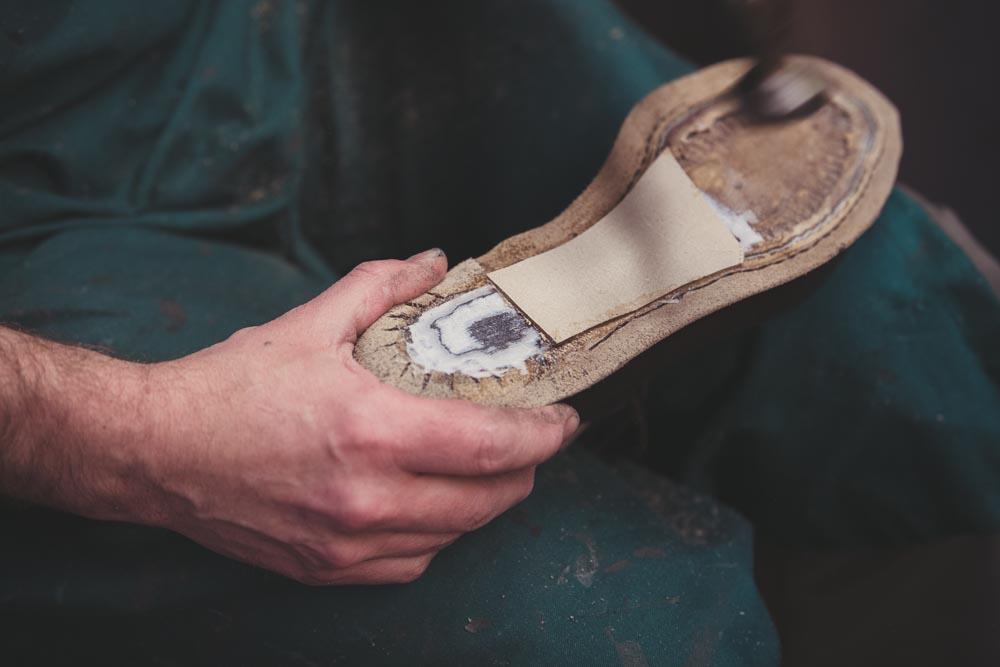
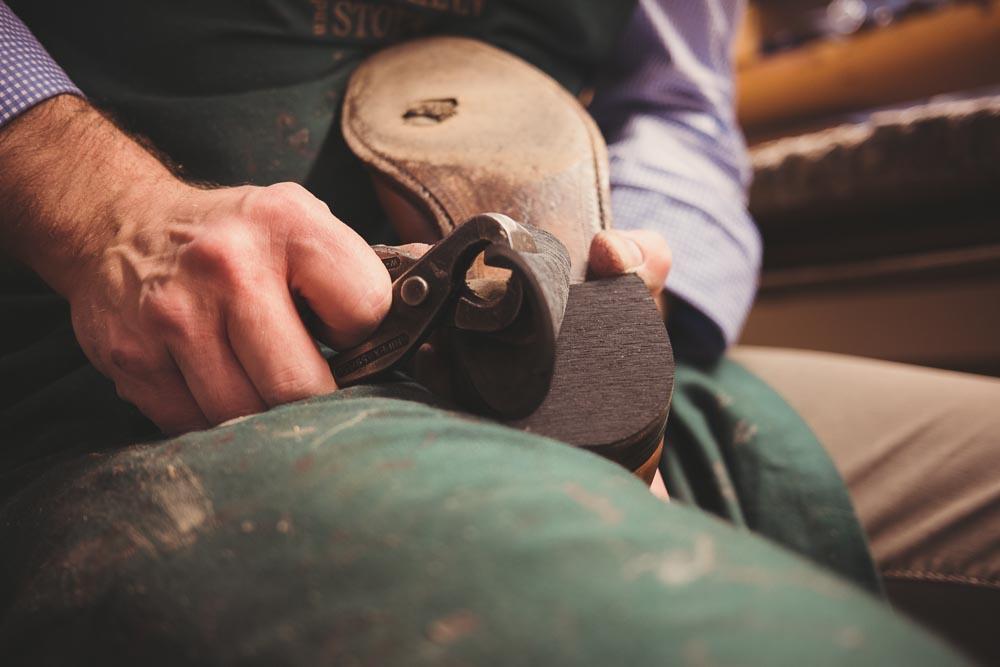
“We make everything by hand on site,” said Vickermann. Since the shoes never leave their manufactory throughout the process, “it is possible for the customer to spontaneously come by and ask about the status of his shoes.”
Finally, the shoes are sealed for protection, finished, and polished to a high gloss.
A Craft Worth Protecting
In this age of mass production, the duo still believes in traditional bespoke shoemaking. “Handmade fashion is an expression of personality, and where traditions and crafts are also kept alive,” Vickermann said.They’ve seen more and more other people appreciating the craft, too. There has been a rise in consumers investing in long-lasting couture and bespoke fashion during the pandemic.
“People attach more importance to sustainability and longevity, as the environment is also becoming increasingly important to them,” Vickermann said. “Good quality definitely means more durability.
“The craft is also being given more attention and admired again, as people also realize that many professions are threatened with extinction.”
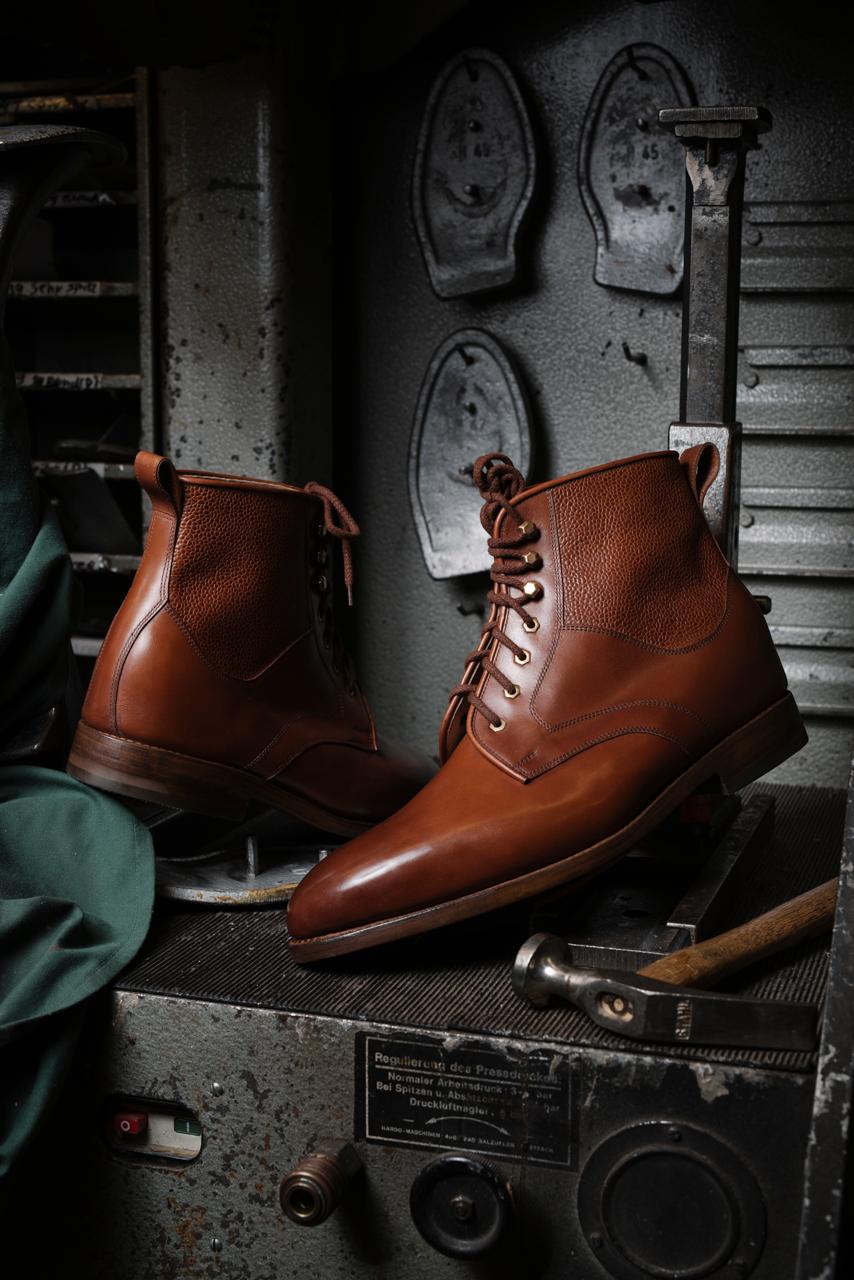
Their business has grown over the years. In the early days, “we both worked as craftsmen, as there were only two of us,” Stoya said. Now they’ve grown to eight employees and have also become a “training company, educating people about what we do, as well as hosting shoe care seminars.”
Vickermann hasn’t made shoes himself in about six years. He’s often on the road, visiting international customers to take measurements and meeting new customers through events. “I feel incredibly comfortable in sales, and I also really enjoy teaching other people about our craft and getting them excited about it,” he said.
These personal relationships are also a unique feature of old-fashioned bespoke shoemaking. “We’ve noticed that our customers are not only concerned with the product, but also with the interpersonal [aspect], which is of course also our top priority,” Vickermann said. “We are ready to visit our customers anywhere in the world, and [give] personal advice ... at any time of the day. ... Only in this way can years of trust be built up.”
During the pandemic, they even expanded their services by going digital, creating an online shop for shoe repairs (ShoeDoc.de). It was important for them to not lose their connections with their clientele.
Of course, nothing beats a face-to-face connection. So if you find yourself in Baden-Baden, stop by Vickermann and Stoya and see for yourself how they are keeping this old-world tradition alive.
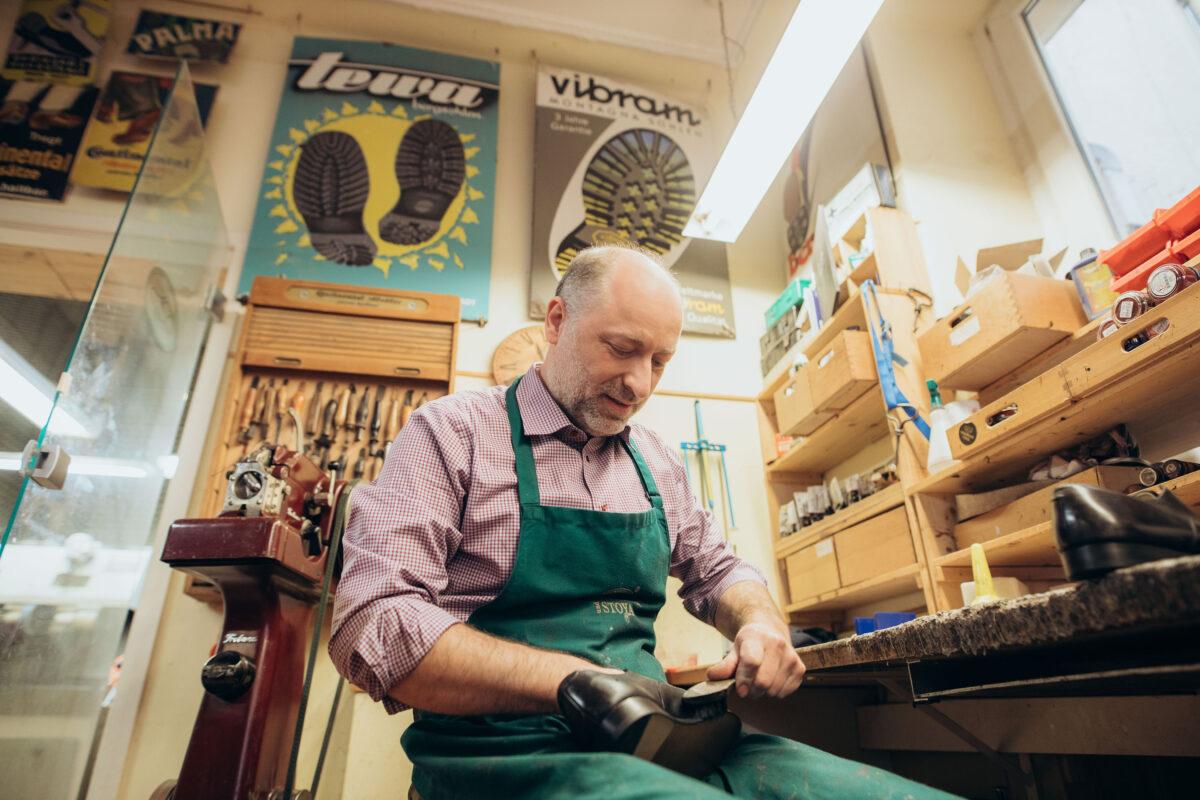