SACRAMENTO, Calif.—A new housing development set to open in Folsom, California, in March is being built with a unique framing technology and design by Japanese homebuilder Sekisui House.
Called Shawood at Folsom, located at 4641 Dehone Circle, just north of East Bidwell Street, the homes offer spacious floor plans spanning up to 4,350 square feet and five bedrooms with oversized kitchens and indoor-outdoor living spaces. There are 41 lots available.
The company showed off its framing system recently during a walk-through of the development. Unlike most conventional homes, where lumber is cut on site and nailed together, Shawood makes a fully laminated, precisely pre-cut product that is bolted together on site. Sekisui uses sustainable imported wood from Finland in its construction.
“What we’ve been doing in the U.S. for decades is conventional two-by-four construction using conventional studs and headers and it’s been done essentially the same since the ’50s, or maybe even longer,” Troy Wood, manager of value engineering for Sekisui House, said. “The post and beam construction is different from the sense that all of our material is imported from Japan, and all of our material is laminated from sustainable wood that’s coming from Finland.
“And because we are an environmentally conscious company, every time we take a tree, we plant two new trees.”
The pre-fabricated lamination method makes the product “very accurate and it’s very strong,” he said.
“The wood is taken to our factory in Japan, where it’s laminated, and then we use precision cutting methods in a factory, where we cut all of our post or beams and all of our studs in a factory so that everything comes out pre-cut for the job,” Wood added.
Wood pointed to a magnitude 9.0 earthquake in Japan in the 1990s to illustrate how strong Sekisui buildings are built.
“We had roughly 177,000 homes that had been built at that point,” he said. “Sekisui House, as a company, went out and looked at all the homes that had been built over the last 30 or 40 years prior to that to confirm that they had no structural damages—every home that we had built, not only did they survive, but they survived with no structural damage.”
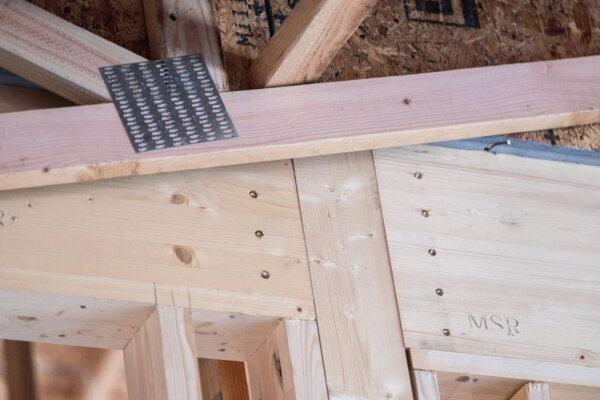
The company says the production of pre-fabricated, accurately cut framing allows for flexibility in customizing layouts and reduces waste. The method maximizes energy efficiency to lower utility costs, too. The framing is also more durable and resistant to weather-related wear and tear, as well as to pests, the company said.
He acknowledged the Sekisui method of construction comes at higher cost, “because it’s a higher-quality product, but that’s part of what we’re creating with our Shawood brand.”
Folsom is the second master-planned community in California to be launched by Shawood. Last year, the brand debuted in the Sommers Bend community in Temecula. Sommers Bend homes start at $1.68 million.
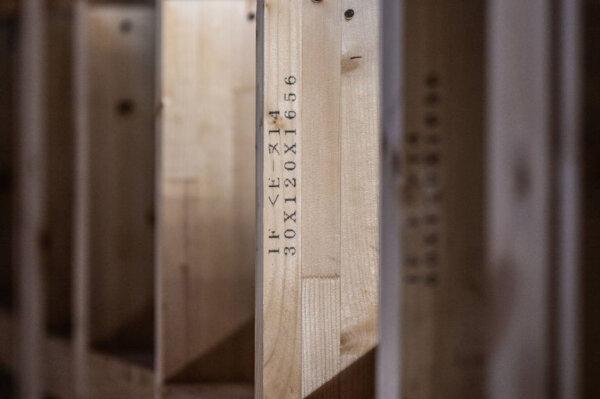
- Zero-energy upgrade options that include solar paneling to provide ample coverage against an outage.
- Prep kitchen.
- Pet wash station.
- Dedicated fitness room.
- Flexible spaces to accommodate a family’s evolving needs include a pocket office, raised loft and media room.
- Aspen: A three-bedroom, four-bathroom home spanning 2,960 square feet.
- Birch: A four-bedroom, five-bathroom home spanning 3,685 square feet.
- Cedar: A five-bedroom, five-bathroom home, with two powder rooms, spanning 3,953 square feet.
- Hazel: A five-bedroom, six-bathroom home spanning 4,346 square feet.
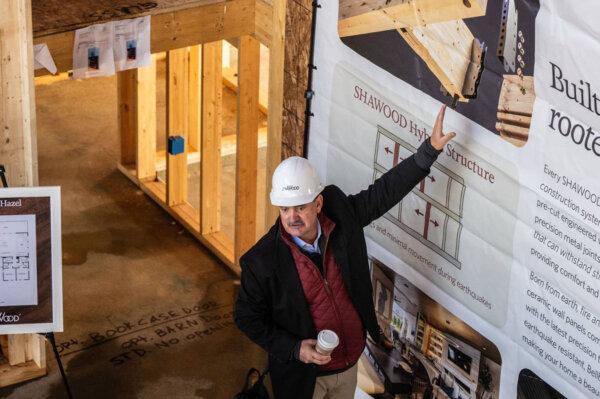