There is a sound in Switzerland unlike any other, and one that rarely crosses the country’s borders. No, I’m not talking about the ticking of millions of timepieces or the jingle of cowbells, but the musical tones created by the Örgeli. The Schwyzerörgeli, as it is properly called, is a type of diatonic button accordion used in Swiss folk music. Örgeli is the diminutive form of the word Orgel (organ). In a country of only 8.5 million people, very few still know how to build the delicate instrument, which consists of about 3,500 separate parts.
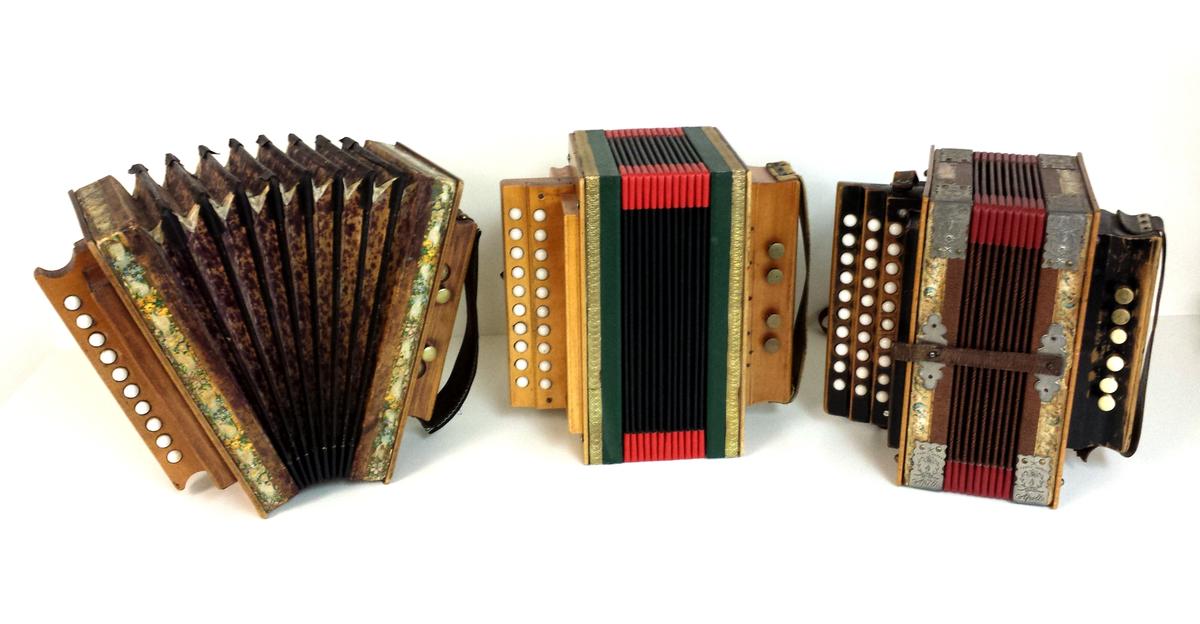
Antique örgelis. Reist AG