LOUISVILLE, Ky.—A rapidly electrifying planet is driving voracious demand for critical minerals, straining supply chains China dominates because it processes and exports 90 percent of some key materials needed for lithium-ion batteries.
There are numerous strategies to domestically source these key materials, including more mining, increased tariffs on Chinese batteries, and incentivizing refining.
“E-waste is the world’s fastest-growing waste steam. The good news is, lithium-ion batteries are infinitely recyclable,” Redwood Materials vice president for government relations and strategic partnerships Alexis Georgeson told state lawmakers, legislative aides, and lobbyists on Aug. 5 during the National Conference of State Legislators (NCSL) 50th Annual Legislative Summit at the Kentucky International Convention Center in Louisville.
The problem is, she said, there’s not enough “infrastructure in place to reuse these minerals, those metals, or to extract them” and many people don’t know their old digital device batteries have value.
The Biden administration has earmarked more than $6 billion in tax credits and inducements to “incentivize processing,” including battery recycling, in 2021’s Bipartisan Infrastructure Law and 2022’s Inflation Reduction Act, said Daniel Shapiro, the Department of Energy (DOE) battery manufacturing & recycling deployment manager.
The DOE offers a menu of competitive matching grant programs with 50- and 30-percent pay shares for state and local governments, including a round of grant “funding opportunities” posted Aug. 1 that it commits $22 million for “smart manufacturing” and $41 million for battery recycling, he said.
Among other efforts to spur domestic battery manufacturing, the administration has increased tariffs on Chinese-made lithium batteries from 7 percent to 25 percent and the Department of Defense has issued a 2027 moratorium on using any batteries manufactured in China.
Georgeson said DOE’s grant programs provide “opportunities for states to further incentivize” battery recycling, but lawmakers across the country are not aggressively capitalizing on these opportunities or adopting laws to promote battery recycling.
Unlike recycling for plastics and paper, which has proven largely unprofitable, recycling lithium batteries is “very different” because they retain value unlike batteries that power “the hydro-carbon economy” where once “it is used, it’s gone forever,” Georgeson said.
Between 95 to 98 percent of critical minerals in lithium batteries can be recovered “so we can get them back into components” for new batteries, creating a local “circular supply chain,” she said.
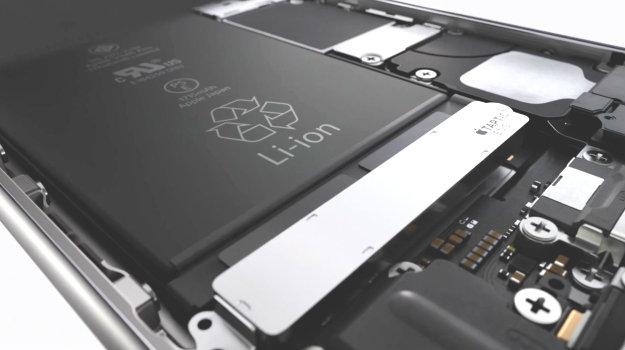
Playing Catch-Up
Founded in 2017 by Tesla co-founder and former chief technology officer J. B. Straubel, Redwood Materials’ Battery Materials Campus is in the same Carson, Nevada, industrial park as Tesla’s EV plant and is the only commercial-scale source of lithium to come online in the United States in decades.The company’s proprietary hydrometallurgy process and rotary calciner produced the first battery anode copper foil in North America, and its campus includes the first commercial-scale nickel mine to open in the United States in a decade.
Redwood has recently built a second campus in the “battery belt” near Charleston, South Carolina, Georgeson said.
The Nevada plant has recycled more than 250,000 EV batteries for Tesla’s plant, she said, noting that number will increase because “some of the early EVs are just starting to be recycled. Every single year, we have more and more coming off the road. We will hit an inflection point in recycling EV battery for EV battery” in a decade if recycling becomes common.
“China had a head start. They have a 20-year lead on us. We’re playing catch-up,” Georgeson said. “The good news is” as the world’s largest consumer, the nation is awash in batteries from all sorts of digital devices with batteries that can be recycled.
Redwood Materials has staged “grassroots events around the country” to inform consumers their old iPhones—Americans throw away 150 million a year, she said—and other digital devices have value and can be recycled.
“We set up shop and collect and recycle those free of charge,” Georgeson said, but there needs to be local capacity to collect and, ideally, recycle the batteries to create a market.
Localizing recycling and extraction “is a great way to lower costs,” create jobs, and enhance national security, she said. “All of the components are still coming from overseas, representing a major risk to national security, sustainability, and [aggravating] the cost factor.”
Shapiro said DOE is “working with local communities and companies” with or without state collaboration in promoting recycling because “the leakage of these materials offshore is a big issue.”
Montana Rep. Steven Galloway (R-Great Falls) noted that lithium-ion batteries “catch on fire, so a lot of recyclers don’t want to take them.”
“Properly packaging and transporting them is a core part of what we do,” Georgeson said. “There’s an extreme safety focus” and best practices can be taught by trainers “showing up at junkyards to help dismantlers.”
Galloway also raised “distance issues” in thinly populated rural areas making recycling financially unfeasible. Most of Montana doesn’t “have the density of usage to make it worthwhile.”
Georgeson said as part of its educational effort, “We’re frequently going into the field and picking up one-off batteries. It is not cost-effective but it is what we are committed to do” in currying “a consolidation” as the industry matures.
Ultimately, however, recycling is just one component of a comprehensive plan to create a closed-loop domestic supply chain for critical minerals, she said.
“In general, this industry is really in its infancy. We must be thinking about the long-term,” Georgeson said. “We can’t just stop at recycling. We have to make the components. We are going to have to mine more. We cannot recycle our way” to domestically sourcing critical minerals.