Researchers have developed a new plastic packaging for fresh food and takeaway by replicating lotus leaves’ resilient and self-cleaning structure.
Lotus leaves are renowned for having some of the most water-repellent sources on earth and are practically impossible to get dirty.
Lead author of the study and Royal Melbourne Institute of Technology (RMIT) PhD researcher Mehran Ghasemlou said that the secret lies in the structure of the leaf’s surface, which is composed of tiny pillars with a waxy coating.
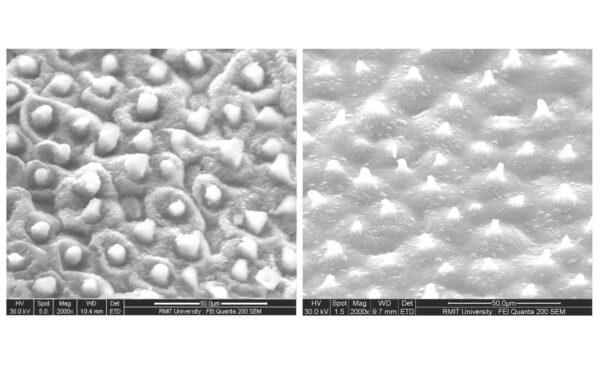
Any water that lands on the leaf remain a droplet, rolling off with the help of gravity. The droplets sweep up dirt as they slide down, keeping the surface clean.
“We’ve replicated the phenomenally water-repellent structure of lotus leaves to deliver a unique type of bioplastic that precisely combines both strength and degradability,” Ghasemlou said in a release.
The team also found that scratches with abrasives and exposure to heat, acid, and ethanol did not cause damage to the material.
Bioplastic is made from organic materials as opposed to petroleum. Likewise, this new plastic is made from starch and cellulose, which are cheap and widely available raw materials.
Unlike most biodegradable or compostable plastics, which require industrial processes and high temperatures to break them down, the researchers found their bioplastic degrades quickly.
“This is reflected in the results from our soil studies, where we can see our bioplastic rapidly breaks down simply with exposure to the bacteria and bugs in the soil,” Ghasemlou said. “The fabrication process does not require heating or complicated equipment.”
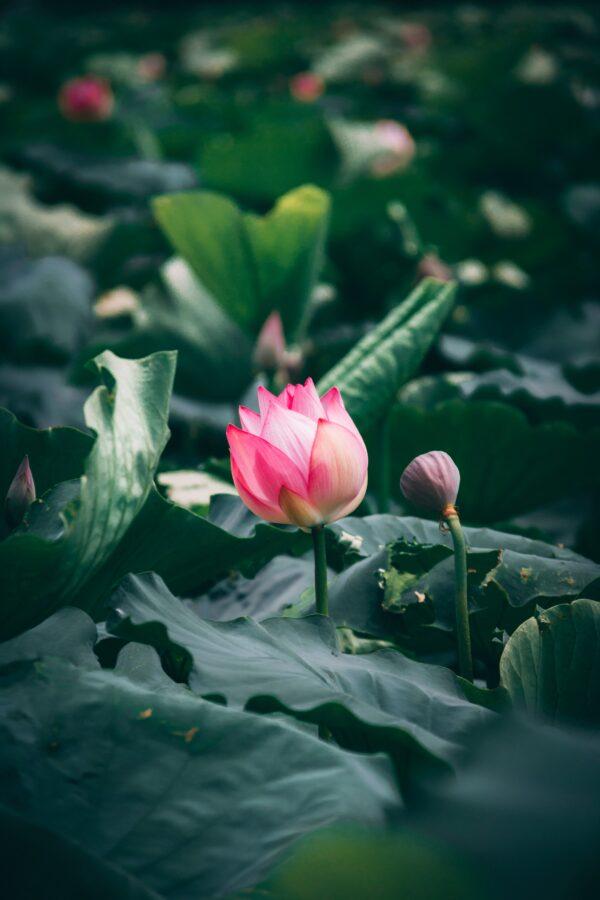
Co-author and professor Benu Adhikari said the design solves key problems of starch-based materials.
“Starch is one of the most promising and versatile natural polymers, but it is relatively fragile and highly susceptible to moisture,” Adhikari said.
“Through our bio-inspired engineering that mimics the ‘lotus effect’, we have delivered a highly-effective starch-based biodegradable plastic.”
Ghasemlou is seeking potential collaborators and is currently liaising with a bioplastic company. Passing the evaluation stage, production of the bioplastic for commercial application will be near.
“We designed this new bioplastic with large-scale fabrication in mind, ensuring it was simple to make and could easily be integrated with industrial manufacturing processes,” he said.